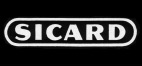
SM-3 Sanivan (1945-1950)
Sicard Sanivan SM-3 with the cover-compressor opened above the load within the hopper
    The model SM-3 Sanivan is one of the great unsung breakthroughs in refuse truck design, and appears to be the first commercially successful refuse truck from Sicard. Ronaldo Boissonnault of Montreal filed the patent in 1945, which was assigned to Arthur Sicard. Production likely began that year or shortly thereafter, and the SM-3 was advertised in the 1946-47 Municipal Index. Boissonnault improved greatly on Irénée Sicard's unloading method by applying hydraulic power directly to the moveable barrier within the body, thus making the SM-3 the first North American rear loader with direct hydraulic ejection, more than a decade before this feature appeared on competitive rear loaders.
    The SM-3 Sanivan employed an all-new packing method, enclosed within a raisable tailgate structure hinged to the main body. Pre-compaction of each hopper load of refuse was achieved by crushing batches of refuse between a cover compressor panel and a moveable compressing wall within the tailgate. Once crushed to maximum density (a hydraulic pressure gauge alerted the operator), the compressing wall was then raised, and the load swept inside by the completed arc of the cover-compressor. Power came from two sets of hydraulic rams mounted outside the tailgate, connected to the panels through gearing and crank arms.
Operating Cycle:
The "Yard-by-Yard" pre-compaction system of the SM-3
|
Loading Position
Cutaway drawing sequence shows packing panels, with hydraulics omitted for clarity. The SS-3 utilized twin pivoting panels with a "pre-crushing" action taking place in the tailgate. Cover-Compressor A is shown here in the full open position, ready to receive refuse in the hopper B. Compressing Wall C is fully lowered, forming a barrier between hopper and previously compacted load.
Unlike the Gar Wood Load-Packer, there was no "loading level" in the hopper B; Sanivan hopper could be loaded until no more refuse would fit.
|
First Stage
Operator commences cycle by pulling and holding a control lever for cover-compressor A, causing rotation through the hopper. As the hopper is swept, the load is "pre-crushed" against the rear face of the compressing wall C. When maximum pressure is achieved, the packing panel stops and the lever is then released. A hydraulic oil pressure gauge was also provided, which would cue the operator that a particular panel had reached its respective limit.
|
Second Stage
Operator next pulls lever which raises the compressing wall C, opening a passageway from the hopper to the storage body. The cover-compressor A is then further actuated, pushing the pre-crushed load into storage body until it reaches its maximum travel limit. Lever is released, which stops cover-compressor in this position.
|
Final Stage
Operator lowers the compressing wall C, thereby closing off passageway and scraping the forward face of cover-compressor A. Compacted load is now retained in body, and cover-compressor may be reversed through hopper, and back to the loading position.
|
SM-3 Packing Cylinder Location
Cutaway drawing below shows location of key features.
Operating cylinders, mounted outside of hopper sidewalls are normally concealed by protective covers.
|
1   Cover-Compressor
2   Cover-Compressor Cylinder
3   Cover-Compressor Sector and 4 Gear
5   Compressing Wall Cylinder and 6 Bellcrank
7   Tailgate Clamp and Lever
8   Packer Control Levers
|
THE PROBLEM OF UNLOADING
    The rear load packer truck was itself a fairly new concept in 1945. With the exception of the British-made Eagle Compressmore rear loader of 1938, ejection discharge was a feature limited to side-load designs such as the Marion Compressor and the Grace packer. Rear loaders, such as the Gar Wood Load-Packer used hydraulic tipping to unload, just like a standard dump truck. Tipping is well suited for dump trucks, which haul heavy, dense material (such as rock or earth) which will easily discharge when the bed is elevated.
    Refuse packer trucks however, hold comparatively light loads that are stuffed tightly into the body. When tipping, the weight of the engine, cab and forward chassis tended to counter that of the load...most of the time. If the weight and density of the load were excessive, the balance was shifted rearward and the front wheels of the truck chassis could come off the ground, stranding the vehicle on its back.
    The taller refuse body has a high center of gravity, even more so when the loaded body is raised. This is further aggravated by the weight of the tailgate structure, raised high above the body during unloading. Since refuse trucks frequently unload on the notoriously poor footing of sanitary landfills, the danger of capsizing was all too real. Capsizing was not only dangerous to the men, it obviously was damaging to the truck and body as well.
    Since the Sanivan has not been made for nearly fifty years, it is often overlooked as the first fully-enclosed rear loader to address this problem using hydraulic ejection to discharge. Sicard also pioneered the use of twin cross-mounted hydraulic cylinders, a feature which has become standard on most modern front loaders.
Figure 1: Loading Position (side, top views)
Cutaway drawing shows folding ejection bulkhead fully retracted at the front of body, ready for loading to commence. The bulkhead consists of three panels 1A, B, C hinged to each other to form a barrier within the body. The uppermost panel is pivotally connected at the roof 2 and bottom section is connected to twin hydraulic cylinders 3A, B mounted to the front of the body. Note in the top view how these offset, cross-mounted cylinders stow away neatly in the space ahead of and and beneath panel 1C. There is relatively little "dead space" in front of the ejector panel assembly. A set of push bars 4 are connected on one end to the lower ejector panel 5. Rearward end of each push bar is rounded 6, and bars lay horizontal on either side of the body floor.
|
Figure 2: Unloading Position (side, top views)
To unload, the tailgate clamps are first released manually by the operator. Then, by pulling a single control lever, the hydraulic cylinders 3A, B are pressurized and begin to slide the lower ejector panel 1C rearward. After a traveling a short distance, push bars 4 contact tailgate structure at 6 and begin to force it up and away from the body. As the cylinders continue extending rearward, the upper sections of the ejector panel 1A, B are pulled along with by lower section. At the full rearward extension, the tailgate is propped fully open, and the three sections of the ejector form a flat surface, disposed at a steep angle which allows any remaining refuse to fall away by gravity.
|
Figure 3: Unloading Position (3D view)
Three-dimensional rear view illustrates sloped surface that is formed by three panels 1A, B, C after full rearward extension of the assembly, as push bars 4 hold tailgate open. Also note adjustable seals at outboard ends of panel sections 7, as well as box-bracing to strengthen body 8, another feature that was to foreshadow modern refuse truck design.
|
    By the end of the 1950s, several side and front-loading refuse bodies were using multiple-stage telescopic cylinders for packing and ejection functions, and in 1960 Heil would use a hydraulic ejection panel in their Colectomatic Mark II rear loader. The use of twin single stage cylinders in the SM-3 Sanivan may have been for economy, or perhaps due to the lack of availability of double-acting telescopic cylinders at the time. Regardless, Sicard had built a highly advanced design for its time, and the first rear load packer to seriously challenge Gar Wood.
The revolutionary SM-3 Sanivan: ejection unloading display at Sicard Montreal factory, February 1946
SELECTED PATENTS
Patent # |
Description |
Inventor |
Assignee |
Date |
US2430973 |
Vehicular load carrier and collector |
Boissonnault |
Sicard |
July 16, 1945 |
11/6/04 (revised 12/13/20)
© 2004, 2020
All Rights Reserved
Photos from factory brochures/advertisements except as noted
Logos shown are the trademarks of respective manufacturers
|
|
|