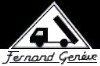
FERNAND GENÉVE
Ivry, France
By Eric Voytko
    In 1935, the Paris-based firm of Fernand Genéve had more than a decade of experience building all manner of vocational truck equipment. This included special refuse collection bodies used by major contractors such as Société Industrielle de Transports Automobiles (SITA), and Cie-Generale des Entreprises Automobiles (CGEA). SITA had began producing their own hydraulic packer bodies a few years earlier, under the direction of Fernand Rey, and was in the process of converting their fleet of 500 hand-loaded trucks to his new automatic Reyloader design. To satisfy the Paris City Council's demand for more modern, hygienic refuse equipment, all contractors would undoubtedly be seeking enclosed compactor trucks like the ones that SITA had introduced.
    Genéve answered the challenge with a new body called Salubra, which roughly translates to mean "healthy". Along with the Reyloader, this new enclosed, self-loading refuse body was one of the first to utilize a packer plate. It was designed by Pierre Rotteé , who assigned the rights to Fernand Genéve in 1934. Unlike the Reyloader, the Salubra had a fixed bucket or trough, the width of the body, allowing two men to load simultaneously. When full, it was mechanically raised within an enclosed passageway and inverted at the uppermost point in the body. The refuse then fell in front of an internal packer plate, powered by double-acting hydraulic rams. These same rams also powered the loading bucket, and the two components worked in unison. When the packer plate retracted, the bucket was raised and dumped. Then, as the packer pushed the load into the body, the empty bucket was lowered back to the ground for the next batch of refuse.
    Though it was not a continuous-loading system, the Salubra represented a marked improvement over the previous hand-loaded trucks which they replaced, in both efficiency and dust control. The first units appeared in Paris in 1935, in service with CGEA, and worked the same streets as the Reyloaders employed by SITA. Thus, while most major cities of the world were still using hand-loaded trucks or even horse drawn wagons, Paris had no less than two competing brands of hydraulic packers collecting refuse within its borders.
DETACHABLE BODIES
    The Salubra body was detachable, allowing cranes located at the transfer station to pluck filled bodies from the truck chassis for emptying, or replacement with an empty unit. Even the tailgate/packer assembly could be removed, transforming Salubra into an open-backed van body. Bodies removed for maintenance or repair could be immediately replaced with a spare. Tipping gear on the truck provided for conventional dumping of the contents, with the tailgate/packer unit lifted clear by cables affixed to the vehicle chassis. Several different hopper styles were produced, seemingly varied by the capacity of the loading trough.
Early-model Salubra at the tip site, discharging its load
Large-hopper Salubra circa 1949
Post-war Salubra with body tilted, tailgate and packer raised clear for discharge of load
THE SALUBRA DETACHABLE CONTAINER SYSTEM
    Special "commercial" model Salubras were built without fixed loading buckets, and instead had open lower sections to receive special rectangular bins of about 1.5 cubic yards capacity. These Salubras are easily identified by their much larger rear hopper enclosure. The bins were wheeled from remote locations within shops, markets, factories or apartments to the street using dollies, and were sometimes linked in trains. Another variant of the Salubra container had built-in wheels that folded away as they were lifted into the body. If needed, a spare container could be left attached to the truck, and hand-loaded on residential routes just like the smaller Salubra.
    Once again, France was at the forefront of refuse collection technology. This was a major advance, considering that the rear-loading American Leach Packmaster container system was still twenty years away. CGEA took great advantage of the Salubra container system, since it collected from many of the business districts in Paris. Even after more modern container systems had arrived, photographs show CGEA Salubras in use well into the 1960s.
    If not for the Second World War, the European refuse body industry may have expanded to even more cities across the Atlantic, instead of the other way around. The Genéve, Salubra, as well as the Reyloader, did resume production after the war, with only minor updates, but both were ultimately eclipsed by more efficient collection bodies of the 1950s and 1960s. Now largely obscured by the passage of time, Salubra pioneered many features that would factor prominently in future designs. Its internal packer plate concept would be replicated on American bucket loaders within a few years, and of course the detachable container concept would soon be universal. Its "up-and-over" method of raising and inverting the bucket also somewhat foreshadowed the use on automated loader systems which emerged three decades later.
SALUBRA DETACHABLE CONTAINER SYSTEM AND PACKER
Ready for loading, the packer plate  (1)  is extended fully forward, retaining refuse within the body. Full container  (2)  is wheeled from collection point to position underneath rear of body, and coupled to pivoting lift arms  (3). As the cycle starts, twin hydraulic rams begin to retract packer plate  (1)  rearward, ready to accept the next charge of refuse. Simultaneously, the lift arms are raised by a set of cables  (4)  attached to the packer plate and guided by rollers  (5)  and  (6). As the bucket is raised, guide pins  (7)  and  (8)  enter tracks  (9)  inside the tailgate, which aid in stabilization. As the bucket nears its uppermost travel  (2b) , it contacts stop pins  (10) , which cause it to be inverted  (2c)  as lift arms reach their upper limit. Note that guide pins at positions  (7b)  and  (7c)  have left the tracks, which allows bucket to pivot. Refuse from the bucket falls behind the fully retracted packer plate and into the hopper.
Next, the rams reverse, and the packer plate pushes refuse into body as empty bucket is lowered back down to street level. With significant modifications, this very same method was used by American top-pack front loaders developed by Western Body & Hoist and Bemars a quarter century later.
The residential versions of Salubra worked in much the same manner as shown above, except that the bucket was permanently attached, and was raised and lowered by endless roller chains instead of the cable-operated lift arms.
|
Post-war Salubra fixed-bucket rear loader, a down-sized version likely designed for easier maneuverability
Genéve Tasseco side loader, with an unknown type of compaction mechanism
SALUBRA VORAX REAR LOADER
    Genéve introduced the Salubra Vorax around 1960, a completely new design with a rotary pulverizer similar to the original 1948 U.S. Roto-Pac . Clearly, the Vorax was intended to replace the antiquated Salubra with a more modern continuous-loading system comparable with other designs then on the market. Vorax is a Latin word, meaning "voracious" or "gluttonous". Obviously, the name was meant to imply that it possessed great prowess at eating refuse. This power came from a direct hydraulic ram drive, which turned the rotor shaft through a ratcheting linkage.
Vorax rotor was fed from a progressively narrowed loading hopper
Side access door showing the rotor drive mechanism
Vorax reciprocating hydraulic ram with ratcheting linkage
SELECTED PATENTS
Patent # |
Description |
Inventor |
Assignee |
Date |
FR45412E |
Perfectionnements aux camions... |
Rotté |
|
February 11, 1932 |
2084656A |
Self-loading refuse vehicle |
Rotté |
Genéve |
March 26, 1934 |
REFERENCES
Vintage Fernand Genéve Literature in PDF at the Classic Refuse Trucks Library
|
7/31/11 (revised 11/23/19)
© 2011
All Rights Reserved
Logos shown are the trademarks of respective manufacturers
Photos from factory brochures/trade advertisements except as noted
|
|
| |