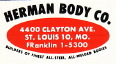
Herman Body Co.
St. Louis, Missouri
by Eric Voytko
    In 1945, Multimillionaire industrialist and speed boat champion Garfield Arthur Wood sold Gar Wood Industries to a group of investors from New York. With that sale went the patents held by the firm, including the famous Load Packer rear load refuse body. The Load-Packer was invented by Gar's brother George B. Wood, who often co-piloted the famous Miss America speedboats. George Wood himself piloted Miss America II to the world water speed record in 1921, and again in 1928 with Miss America VII.
    The Ram-Pak was designed by George Wood independantly, and was not assigned to any manufacturer. It was initially built and sold by the Herman Body Company of St. Louis, Missouri (shown above) starting in 1954. Wood's design was among the first wave of rear loaders to follow the wake of his Load-Packer, during a time when the market was growing for compaction-type refuse trucks. More significantly, Wood's truck represents one of the few American rear loaders to feature continuous-loading type packer mechanism, allowing for uninterrupted loading of refuse by the crew. At the time, continuous loaders of the pre-war Ochsner and Rey type were appearing in greater numbers in Europe, and would enjoy much success there in years to come. However, the U.S. school of design was then heavily favoring intermittent or batch type loaders, with the big three (Gar Wood, Heil and Leach) all offering unique variations by mid-decade.
    The Ram-Pak was designed to pre-crush refuse in the tailgate, a feature shared with another of its competitors, the Sicard Sanivan. Pre-crushing was seen as desirable in this era before full-eject bodies became universal, and rear loaders lacked the compaction power that would come in later years. Despite the novel concept of this design and a variety of improvements, it would however ultimately fail to entrench itself in the increasingly competitive U.S. market, and disappeared after little more than a decade.
HOW IT WORKED
The Ram-Pak utilized a sweeper blade (green highlights) and crusher blade (red highlights) working in conjunction, powered through linkage by a single hydraulic cylinder. Basically, as these drawings will show, the refuse is swept forward by the sweep panel where it is then compacted against the body structure and held in this position. Successive cycling of the mechanism causes the previously crushed load to be forced into the storage body ahead of the incoming load.
In top drawing, refuse is ready to be loaded over the false floor (13), falling into the hopper (14) ahead of the sweep panel (1). Note the retractable skirt (1a) attached to the sweep panel, and concealed beneath the false floor. A pair of pivoting links (2) on either side of the inner tailgate are connected push bars (3). Push bars are connected at their upper ends to a crank shaft (5) which is turned by the main cylinder (4). The crank shaft simultaneously operates the crusher blade (6) through a compensating link (7) and then a toggle linkage consisting of: rocker panel (8) and a pair of "lost motion" links (9) and (10).
The small illustration (middle left) shows a detail of the sweep panel (1) with skirt (1a) as it extends out from beneath false floor (13) as cycle initiates. This skirt prevents refuse from falling behind the sweep panel while it is in motion, allowing uninterrupted loading of the hopper. On the return trip, refuse is scraped off of skirt by lip (12, lower drawing) and falls back into hopper (14) in front of retracting sweep panel.
In the lower drawing, the main cylinder (4) has fully extended, causing the sweep panel (1) to scrape the hopper floor (15) and advance the load to a point between the crusher blade (6) and the anvil (16). Lost motion linkage (9 &10) allows crusher blade to lag slightly behind the advancing sweep panel, thereby holding any pre-crushed refuse in place until slack in chains (11) is used up, causing crusher blade to fully open. Even with sweep panel fully forward, refuse may be continuously loaded since skirt has extended to prevent refuse from falling into the area (14) behind the panel.
In the next cycle, main cylinder would (4) retract, pushing the sweep panel rearward to the first position and lowering the crusher blade to pre-pack refuse between blade (6) and anvil (16). Bypass valves within the compensating cylinder (7) open to relieve any excess pressure in the event that an incompressible object (such as concrete block) were to become lodged under the crusher. The entire cycle was designed to be automatic and continuous, and each successive motion of the sweep panel (1) pushing a small batch of refuse under the crusher (6) while advancing the previously crushed batch into the body. This was a novel concept in 1954 among rear loader designs, which typically did not begin compressing the refuse until the body became filled.
|
    Some of the features mentioned above, such as the compensating link (7) and lost motion linkage (9 & 10) and chains may not have actually been used in production models. Barring the future discovery of any Herman factory literature or photos, these details will remain unclear. It may be observed that the single hydraulic cylinder would seem to be over-taxed in its duties, having to lift, pack and crush the refuse. This would be especially true as the body become loaded. Also, the false floor design seems to leave the vehicle with a very shallow hopper area, even for a continuous loader. Perhaps for these reasons, poor sales or other factors currently unknown, Herman Body Company seems to have discontinued the Ram-Pack after a very short run. However, George Wood licensed his designto Daybrook Hydraulic in 1957, after which and some significant improvements would follow.
    In Canada, the rights to this design were assigned to Phil Wood Industries of Windsor, Ontario. The company namesake was also a brother of Garfield Wood. These Canadian models which were sold under the name Wood Load Crusher, appear to be identical to the American Ram-Pak. It is unknown how long the Wood Load-Crusher was produced.
|
REFERENCES
Daybrook page at Classic Refuse Trucks
|
SELECTED PATENTS
Patent # |
Description |
Inventor |
Assignee |
Date |
US2767867 |
Refuse Vehicle Loading Device |
Wood |
|
May 7, 1954 |
4/2/05 (revised 8/29/09)
© 2005
All Rights Reserved
Logos shown are the trademarks of respective manufacturers
Photos from factory brochures/trade advertisements except as noted
|
|
| |